部品を加工するための3つのプロセス方法
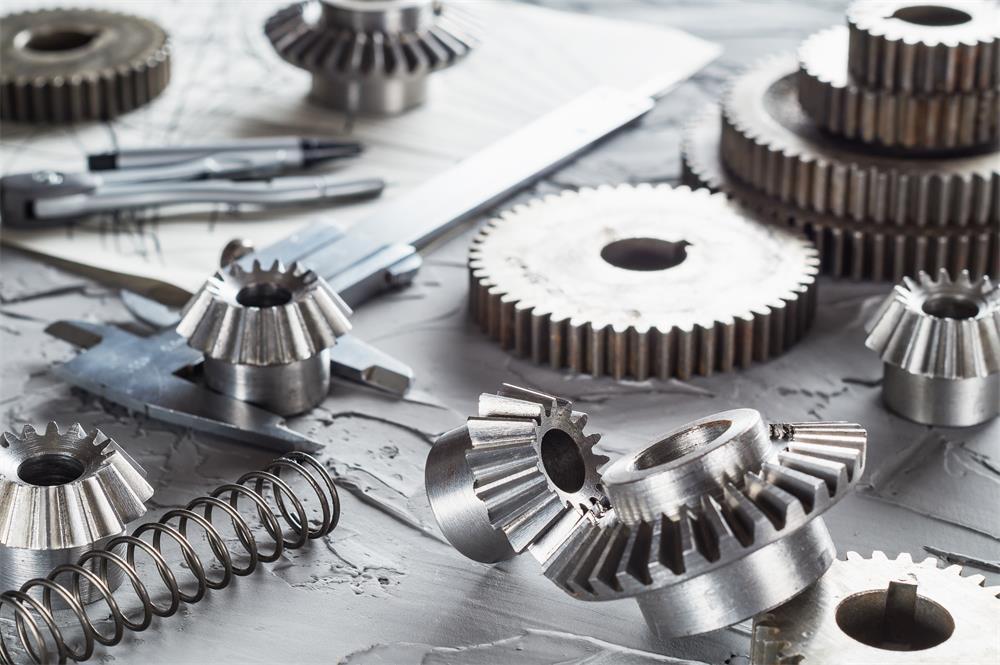
機械部品を機械加工する過程で、技術基準と正しいパラメータに従って部品のサイズ、サイズ、位置、および形状を変更することは、機械部品の機械加工プロセスと呼ばれることがよくあります。機械部品の加工工程は生産工程の重要な部分であり、生産工程全体、さらには製品の品質に直接影響します。機械部品の加工には、次の 3 つの加工方法があります。
材料除去製造工程
材料除去製造プロセスは、特定の方法でワークピースから余分な材料を除去して、必要な形状とサイズの機械の基本部品を取得することです。このタイプのプロセスでは、ワークピースの表面に十分な余分な材料が必要です。材料除去の過程で、ワークピースは徐々に理想的な部品の形状とサイズに近づきます。原材料またはブランクの形状とサイズの違いが大きいほど、より多くの材料が除去され、材料の損失が大きくなり、処理中に消費されるエネルギーが大きくなります。場合によっては、失われた材料の量が部品自体の量を超えることさえあります。
材料除去プロセスの材料利用率は低いですが、依然として部品の品質を向上させるための主要な手段であり、加工適応性も高く、製造で最も広く使用されている加工方法です。材料除去プロセスと材料成形プロセスの組み合わせにより、原材料の消費を大幅に削減できます。最先端技術(精密鋳造、精密鍛造など)の開発により、材料の利用率をさらに向上させることができます。生産量が少ない場合、材料成形工程への投資を抑えるために、単純に材料除去工程を採用することも経済的で合理的です。
材料除去技術には、従来の切削加工や特殊加工など、さまざまな加工形態があります。
切削加工とは、金属切削工具を使用して、工作機械のワークピース (ブランク) の余分な金属を除去し、ワークピースの形状、サイズ、および表面品質が設計要件を満たすようにするプロセスです。切削プロセス中、工具と工作物は工作機械に取り付けられ、工作機械は一定の規則的な相対運動を達成するために駆動します。ツールとワークピースの相対移動中に、余分な金属が除去され、ワークピースの機械加工面が形成されます。一般的な金属切削加工方法には、旋削、フライス加工、平削り、ブローチ加工、研削加工などがあります。金属の切削加工には、力、熱、変形、振動、摩耗などの現象があります。加工工程や加工品質に一定の影響があります。
特殊加工とは、電気エネルギーや光エネルギーなどを利用して材料を除去する加工方法のことです。放電加工、電気化学加工、レーザー加工などがあります。EDMは、工具電極と電極の間に生成されるパルス放電現象を使用して、加工目的を達成するために被削材をアブレーションします。加工中、加工物電極と工具電極の間に一定の放電ギャップがあり、直接接触するのではなく、加工に力がなく、あらゆる機械的特性を持つ導電性材料を加工できます。技術面では、複雑な形状の内輪郭面を加工し、その加工の難しさを外輪郭加工に変換できることが主な利点であるため、金型製造において特別な役割を果たします。 EDM は切りくず除去率が低いため、製品の形状加工には一般的に使用されません。
素材成形の製造工程
材料成形の製造プロセスでは、主にモデルを使用して原材料を部品またはブランクにします。素材がスクラップになる過程で、形、大きさ、組織状態、さらには結合状態まで変化していきます。一般に成形精度が高くないため、ブランクの製造には素材成形製法が用いられることが多い。複雑な形状の部品の製造にも使用できますが、精度はそれほど要求されません。材料成形工程の生産効率が高い。一般的に使用される成形プロセスには、鋳造、鍛造、粉末冶金などがあります。
キャスト
鋳造は、部品の形状とサイズに適した金型キャビティに液体金属を流し込み、冷却および凝固後にブランクまたは部品を得るプロセスです。基本的な技術プロセスは、モデリング、製錬、注入、洗浄などです。合金鋳造中の金型充填能力、収縮、およびその他の要因により、鋳物に不均一な構造、収縮、熱応力、および変形が生じる可能性があり、鋳物の精度、表面品質、および機械的特性が低下します。それにもかかわらず、その強い適応性と低生産コストのために、鋳造加工は依然として広く使用されています.形状が複雑で、特に内部の空洞が複雑なラフな部分は鋳造に使われることが多いです。
現在、生産に一般的に使用されている鋳造方法には、通常の砂型鋳造、インベストメント鋳造、金型鋳造などがあります。
鍛造
鍛造と板金プレス加工を総称して鍛造と呼びます。鍛造は、鍛造設備を使用して、加熱された金属に外力を加えて塑性変形させ、特定の形状、サイズ、構造の部品ブランクを形成することです。鍛造ブランクの内部構造は緻密で均一です。金属の流線分布が合理的で、部品の強度が向上します。そのため、鍛造は、総合的な機械的特性が要求される部品のブランクの製造によく使用されます。
鍛造は、自由鍛造、型鍛造、タイヤ型鍛造に分けられます。
自由鍛造とは、上下のアバットメント鉄の間に金属を挟み込み、金属を塑性変形させることで、自由流動により実現します。一般に、バッチサイズが小さく単純な形状の鍛造品を製造するために使用されます。
模型鍛造とは、鍛造用金型の型穴に金属を入れて変形させることです。金属の塑性流動は、ダイ キャビティによって制限されます。成形効率が高く、精度が高く、金属の流線分布がより合理的です。ただし、金型の製造コストが高いため、通常は大量生産に使用されます。自由形状モデルの鍛造に必要な鍛造力は大きく、大きな鍛造品の鍛造には使用できません。
タイヤ金型鍛造とは、自由鍛造設備でタイヤ金型を用いて金属を鍛造することです。タイヤ金型は、製造が簡単で、低コストで、成形が便利ですが、成形精度は高くありません。それらは、精度要件の低い小さな鍛造品を製造するためによく使用されます。
粉末冶金
粉末冶金は、金属粉末または金属粉末と非金属粉末の混合物を原料として使用し、金型のプレスおよび焼結プロセスによって特定の金属製品または金属材料を製造するプロセスです。特殊な金属材料だけでなく、切削加工をほとんど行わずに金属部品を製造することができます。粉末冶金の利用率は95%に達し、切削加工の入力を大幅に削減し、生産コストを削減できるため、機械製造でますます広く使用されています。粉末冶金で使用される粉末材料は高価なため、成形時の粉末の流動性が悪く、部品の形状やサイズには一定の制限があります。粉末冶金部品には一定量の小さな気孔があり、その強度は鋳造または鍛造品よりも約20%〜30%低く、可塑性と靭性も劣っています。
粉末冶金生産の技術プロセスには、粉末の準備、配合、プレスと成形、焼結、成形などが含まれます。その中で、粉末の調製と混合プロセスは、通常、粉末を提供するメーカーによって完了されます。
材料累積製造工程
微少要素の重ね合わせでパーツを徐々に積み上げて成長させる素材集積製法。製造工程では、部品の三次元立体モデルデータをコンピュータで処理し、材料の蓄積プロセスを制御して目的の部品を形成します。このタイプのプロセスの利点は、ツール、固定具、およびその他の生産準備作業を必要とせずに、複雑な形状の部品を形成できることです。
製作した試作品は、デザイン評価や入札、サンプル展示などにご利用いただけます。したがって、このプロセスはラピッドプロトタイピング技術とも呼ばれます。ラピッドプロトタイピング技術は、製品サンプルの製造、金型の製造、少数の部品の製造に使用されます。企業の製品が市場に迅速に対応し、企業の競争力を向上させるために、新製品の開発を加速し、コンカレント エンジニアリングを実現するための有効な技術となっています。
ラピッドプロトタイピング技術の急速な発展は非常に速く、現在、主に光硬化法、積層製造法、レーザー選択焼結法、溶融蓄積造形法など、いくつかの方法が応用段階に入っています。最初のラピッド プロトタイピングが商用化されました。テクノロジー。
機械部品の加工プロセスは、機械加工製造技術に従う必要があり、生産プロセスは実際の状況に応じて決定する必要があります。上記を読んだ後、機械部品について詳しく知りたい場合は、より詳細なソリューションについてお問い合わせください。
専門部品メーカーとして豊富な生産実績があります。精緻な生産管理を重視し、万全の品質検査体制を確立し、高品質な製品をお届けします。また、思慮深いワンストップ サービスを提供し、お客様のニーズに応じて効果的なソリューションを開発します。当社の機械部品にご興味がございましたら、すぐにご連絡ください。